A brief history of DO-254
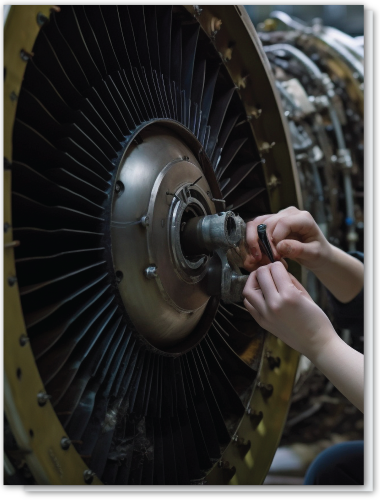
The DO-254 Guideline
DO-254, also known as "Design Assurance Guidance for Airborne Electronic Hardware," is a guideline developed by the Radio Technical Commission for Aeronautics (RTCA). It was first published in 2000 to address the development and certification of complex electronic hardware used in Avionics systems. DO-254 provides guidance for the design, verification, and validation of airborne electronic hardware to ensure its safety, reliability, and compliance with regulatory standards.
Why was DO-254 Developed?
Key to DO-254's initial concept was standardizing the approach and subsequent framework for the development and certification of airborne electronic hardware, allowing Avionics and aerospace professionals to manage the complexities associated with hardware design and ensure it meets the safety and reliability requirements necessary for its use in aircraft. Compliance with DO-254 is required by regulatory authorities such as the Federal Aviation Administration (FAA) and the European Union Aviation Safety Agency (EASA) for certifying hardware used in avionics systems. An important note: While DO-254 is applied differently by the FAA and EASA, both regulatory committees have documented a harmonized approach to the application of DO-254 in AC/AMC 20-152A which clarifies and completes DO-254 guidance.
By establishing a set of guidelines and best practices, DO-254 provides the reference point for Avionics hardware development that ensures compliance with stringent regulatory requirements. It enhances the consistency, quality, and reliability of electronic hardware while facilitating a more efficient certification process. Thus, DO-254 serves as a crucial tool for the aviation industry, enabling the development of safe and reliable Avionics systems that meet the rigorous, rightly so, standards of airworthiness authorities.
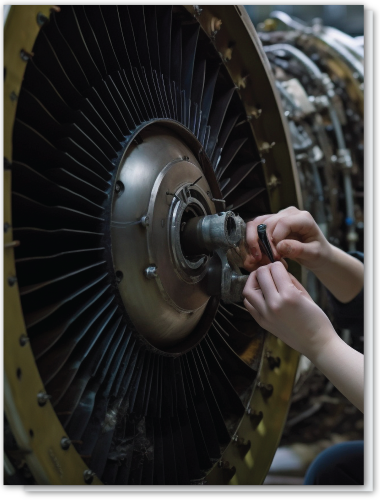
Common Challenges and Best Practices for DO-254
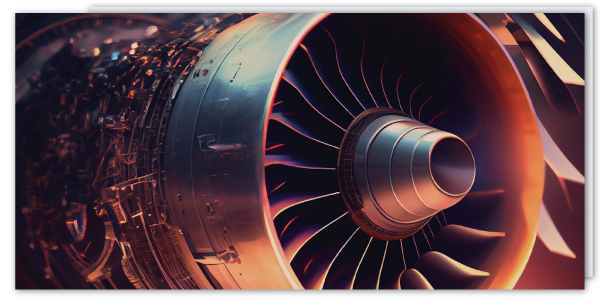
Key Terms in DO-254
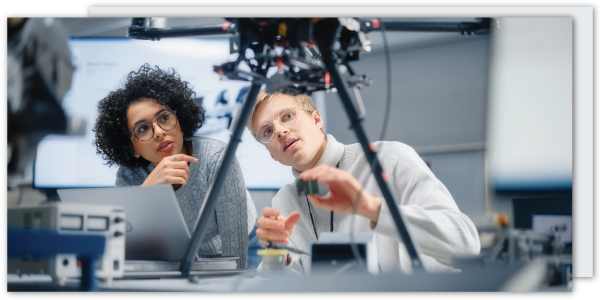
Coordination & Communication
Hardware and software development teams should maintain open communication and coordinate efforts throughout the development lifecycle. Regular meetings, joint reviews, and shared documentation facilitate efficient integration, and that consistent and clear collaboration enables the identification of potential issues or conflicts early on, allowing for timely resolution and alignment of hardware and software requirements.
Interface Definition and Verification
Clearly defining hardware-software interfaces is crucial for seamless integration. Hardware and software teams should collaborate to define interface requirements, including data formats, timing, and error handling. Verification activities should include interface testing to ensure compatibility and proper functionality. By validating the interfaces, any potential mismatches or communication issues can be identified and resolved, ensuring smooth interaction between the hardware and software components.
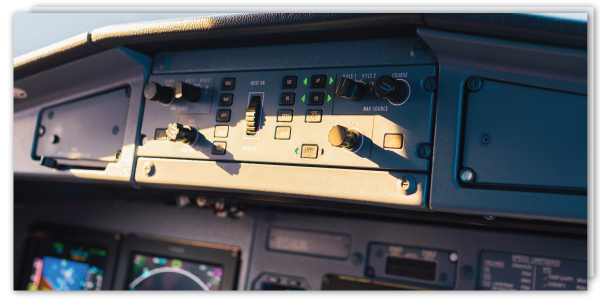
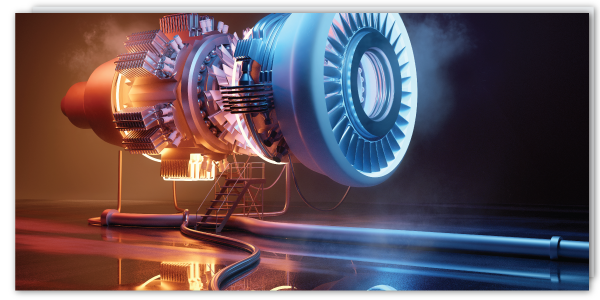
Configuration Management
Effective configuration management is essential for managing changes and versions of both hardware and software components. Consistent configuration control ensures that hardware and software revisions remain synchronized and compatible during integration. Configuration management tools and processes help track and manage the different versions of hardware and software, allowing for traceability and maintaining the integrity of the integrated system.
Joint Testing and Integration Testing
Hardware and software integration testing should be planned and executed collaboratively. Joint testing activities, including hardware-in-the-loop (HIL) and software-in-the-loop (SIL) testing, help identify and resolve integration issues early in the development cycle. These testing approaches allow for the verification of the integrated system's functionality, interaction, and performance. By conducting joint testing and integration testing, potential bugs, errors, or performance gaps can be detected and addressed promptly, ensuring the robustness and reliability of the avionics system.
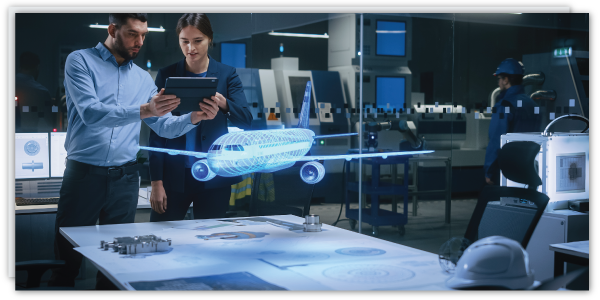
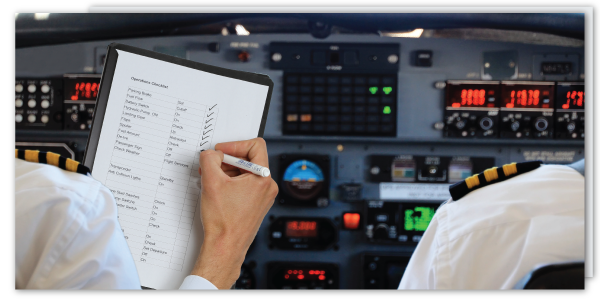
Traceability and Documentation
Maintaining traceability between hardware and software requirements, design artifacts, and verification results is critical. Consistent documentation and traceability records enable efficient certification and provide a clear understanding of the integrated system's functionality and safety. Proper traceability ensures that any changes or modifications made to the hardware or software can be traced back to the respective requirements, allowing for comprehensive impact analysis and ensuring compliance with DO-254 and DO-178C standards.
Ready to become a DO-254 expert?
Fill out the form below and we'll get started on your DO-254 Training Solution